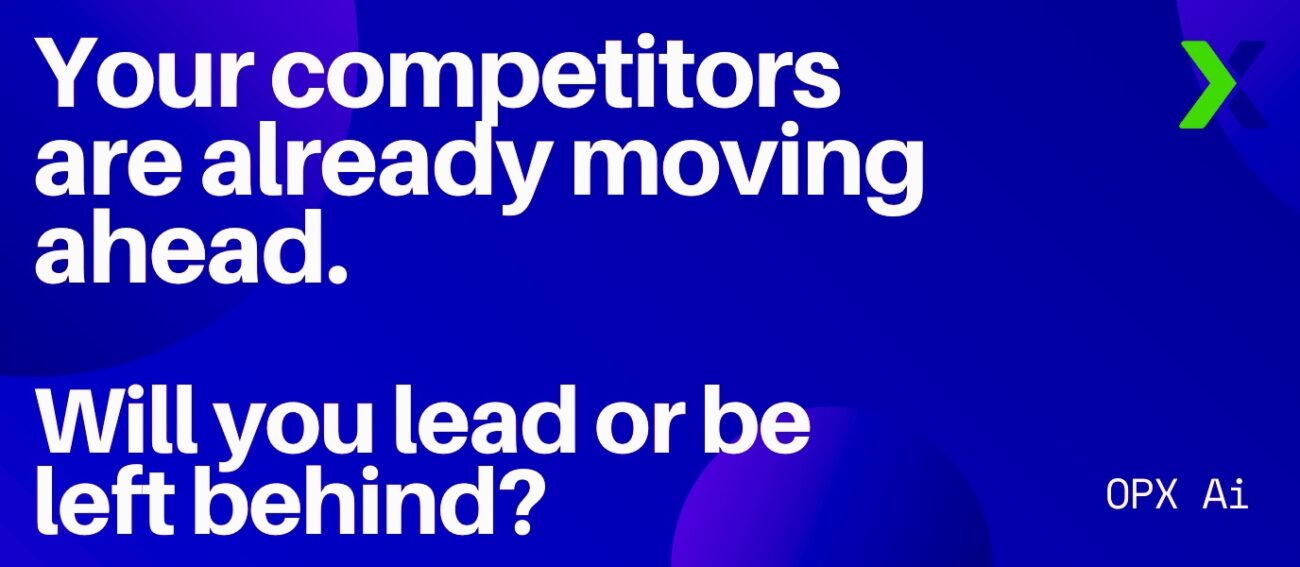
The Future of Oil & Gas Operations: Integrated & AI-Driven
The 2025 Mandate: Digitalization or Decline
The upstream oil & gas industry is entering a pivotal period from 2025 to 2030. Volatile markets, sustainability pressures, and an aging workforce are pushing operators to rethink how they run their fields. “Operations of the Future” is no longer a buzzword but a business imperative. In fact, digitizing operations could unlock $250 billion in value for upstream oil and gas by 2030. Companies that leverage AI-driven automation, data integration, and remote operations stand to gain huge efficiency and revenue boosts. On the flip side, failing to adapt is perilous – roughly 70% of digital initiatives falter, wasting hundreds of billions of dollars, and energy executives now rank failed digital transformation as their #1 business risk. In a margin-tight, carbon-constrained world, embracing digital tech isn’t just about efficiency gains – it’s about survival. As one industry report warns, the divide between digital leaders and laggards can mean the difference between market leadership and irrelevance. The message is clear: upstream operators must evolve now or risk getting left behind.
Major operators have launched multi-year “Operations of the Future” programs to embed digital technologies into base business goals. The sample roadmap above (2025 priorities) shows initiatives like expanding IOC dashboards for chemical management, aligning governance to cut lost production downtime, and scaling digital oilfield solutions across assets. Such plans underscore that integrating IOCs and AI-driven workflows is becoming a core strategic priority, not just an experiment.
Integrated Operations Centers: The New Nerve Center
At the heart of this transformation is the Integrated Operations Center (IOC) – a modern, centralized control hub that coordinates assets in real time. An IOC is more than a fancy control room; it’s an operations nerve center where multidisciplinary teams monitor and manage field operations remotely, aided by AI and advanced analytics. By uniting formerly siloed functions (production, maintenance, engineering, etc.) under one roof, IOCs enable faster, smarter decisions and “manage by exception” workflows. For example, Petroleum Development Oman is developing an IOC to oversee 75 facilities across the country from a single location, centralizing dashboards and expertise so that all assets can “collaborate” and be supervised even when local sites are unmanned at night. The IOC breaks down silos between different SCADA and control systems, creating a single source of truth that finally makes company-wide predictive maintenance and optimization possible. In essence, an IOC serves as the eyes and ears of the operation, aggregating data streams and alarms from across the field into one integrated view.
Crucially, IOCs enable a shift to remote and autonomous operations. In cutting-edge projects like Aker BP’s Yggdrasil development in the North Sea, entire platforms are being designed for fully unmanned or low-manned operation, with all wells and facilities controlled from an onshore IOC. This approach drastically reduces the personnel needed offshore and lowers HSE risk and operating cost. For operators, the ability to run assets with minimal on-site staffing is a game-changer. Early adopters report dramatic efficiency gains – one major operator achieved a 3× increase in well surveillance efficiency by using an AI-powered IOC, allowing a single operator to effectively monitor 150+ wells (up from a few dozen), with anomaly detection algorithms flagging issues across the fleet. This resulted in higher well uptime, fewer site visits, and a shift from reactive firefighting to proactive asset management. Similarly, companies deploying IOCs with integrated analytics have cut lease operating expenses by optimizing energy use and maintenance schedules across their fields. In short, the IOC is becoming the blueprint for upstream “operations of the future,” enabling central control of widely distributed assets, around-the-clock remote monitoring, and tighter operational control than ever before.
AI-Powered Automation: From SCADA Data to Smart Decisions
The backbone of digital oilfield operations is the vast array of SCADA systems and sensors already in place. SCADA (Supervisory Control and Data Acquisition) systems gather real-time data from wells, pipelines, and plants, while historian databases like AVEVA PI store decades of operational data. Traditionally, these systems generated tons of data but not necessarily better decisions. That’s changing with AI. Machine learning algorithms can devour SCADA/PI data and uncover patterns or anomalies invisible to human operators. In other words, AI turns raw data into actionable intelligence, powering everything from predictive maintenance alerts to automated control optimizations.
Remote operations are particularly enhanced by AI analytics. SCADA systems are “the backbone of remote operations”, but legacy implementations often suffer from cluttered screens and alarm overload that hinder performance. By applying AI, companies are simplifying and smartening their SCADA setups – for instance, one operator partnered with specialists to redesign their Ignition SCADA dashboards, using AI to filter noise and highlight important anomalies, which streamlined real-time decision-making in the control room. AI can intelligently prioritize alarms and even execute certain control actions autonomously, reducing the burden on human operators. The result is a 50% improvement in operator efficiency and much faster response times to issues, as reported with AI-augmented SCADA monitoring. With modern IOCs, engineers can supervise a far greater scope of assets because AI is handling the routine monitoring – only true exceptions are brought to the team’s attention (the “operate by exception” model).
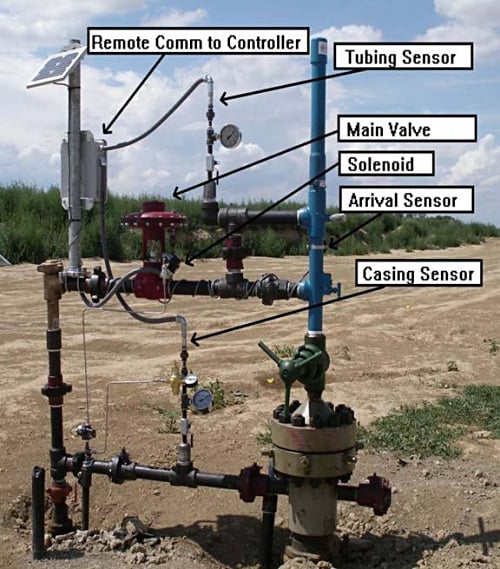
Remote wellheads equipped with solar-powered plunger lift controllers and sensors. These onshore gas wells have pressure sensors on tubing/casing and wireless transmitters (blue boxes), enabling continuous data collection for AI optimization.
A digitally enabled wellhead plunger lift system with IoT sensors and automated controls. Tubing and casing pressure sensors, an arrival sensor, and a solar-powered wireless controller feed data to the SCADA system (labels). AI analytics can leverage this data to optimize the plunger lift cycles in real time. In one deployment, data-driven plunger optimization tool increased gas output by up to 30% across 4,500 wells. OPX Ai similarly reported a 20% production uplift and 30% reduction in downtime after applying AI to plunger lift operations – a clear testament to how automation of field equipment can boost production and reliability.
Artificial Intelligence is also unlocking optimization opportunities in day-to-day production that were previously unattainable. For example, AI-based analytics can continuously tune artificial lift settings (gas lift injection rates, pump speeds, plunger timing) in response to changing well conditions. This dynamic optimization leads to higher output and less downtime compared to static, human-set schedules. Field trials have shown 15–25% increases in productionthrough real-time AI optimization of wells. Likewise, AI can coordinate surface facility operations (separators, compressors, etc.) for optimal throughput, something especially valuable as companies push assets to operate at the edge of their design envelope. All of this is made possible by tapping into the rich streams of data from SCADA and PI – data that most operators already have, but which gains new life when fed into machine learning models.
Predictive Maintenance: From Reactive to Proactive
Unplanned downtime is the enemy of upstream profitability. Legacy maintenance practices often rely on scheduled inspections or reacting to failures after they occur – an approach that leads to costly outages. AI is changing this paradigm with predictive maintenance, using algorithms to forecast equipment issues before they happen so that operators can fix them proactively. The business case is compelling: a single hour of downtime can cost an oil producer on the order of $500,000 in lost production. Industry-wide, unplanned downtime costs upstream companies an average of $38 million per year in lost output (roughly 27 days of downtime per year for a typical operator). Preventing even a fraction of that has huge bottom-line impact. By deploying AI-driven early warning systems, operators are seeing major reductions in failures and downtime.
Real-world results already confirm the value. Shell, for instance, uses AI to monitor over 10,000 critical equipment items (pumps, compressors, valves) across its operations. Their predictive maintenance system analyzes more than 3 million data streams in real time, issuing ~15 million predictions per day about equipment health. The payoff: Shell achieved a 35% reduction in unplanned downtime (boosting overall uptime by ~5%) and cut maintenance costs by 20% – saving about $2 billion per year by avoiding breakdowns. In one case, the AI models detected dozens of control valves in a refinery that were degrading, allowing repairs to be made during planned stops and averting a potential unplanned shutdown. These kinds of wins illustrate how AI can catch subtle warning signs (vibration anomalies, pressure deviations, temperature spikes, etc.) that human operators or basic alarms might miss. By fixing problems early, companies not only save on repair bills but also avoid secondary costs like safety incidents, environmental spills, and production shortfalls.
Today’s upstream Integrated Operations Centers are often equipped with AI-driven dashboards that flag developing issues across wells and facilities. For example, anomaly detection algorithms can continuously scan sensor trends to alert engineers that a certain rod pump is showing early signs of stress, or a remote generator’s performance is drifting – allowing intervention during the next scheduled crew visit rather than a catastrophic failure later. Early adopters of these AI maintenance tools report 30–40% reductions in equipment failure incidents and similar drops in maintenance expenses. OPX Ai has noticed that our clients have achieved 5–30% downtime reduction through predictive maintenance programs. In operational terms, this means millions in prevented losses and a far more reliable operation. It also frees up maintenance teams to focus on strategic improvements instead of constantly “fire-fighting” emergencies.
Why OPX Ai is the Optimal Partner for Operators
To capitalize on these technologies, oil and gas operators need more than generic IT solutions – they need industry-tailored expertise. OPX Ai has emerged as a best-fit partner for upstream operators driving digital transformation. The company combines deep petroleum engineering know-how with cutting-edge AI capabilities, delivering solutions purpose-built for oilfield operations. With 35+ years of hands-on upstream experience (especially in artificial lift and production ops) blended with AI specialists, OPX Ai bridges the gap between traditional field operations and advanced analytics. This means their tools are designed for real-world oilfield conditions and constraints, not just lab algorithms.
OPX Ai’s portfolio covers the key pillars of the digital oilfield: Integrated Operations Centers, predictive maintenance, and production optimization. They don’t just set up an IOC control room and hand it over; OPX provides end-to-end support, from integrating legacy SCADA and PI systems to developing AI models and retraining staff on new workflows. The focus is on delivering turn-key improvements, not more data overload. For example, an OPX Ai-designed IOC features centralized, AI-powered remote operations with built-in anomaly detection and automated workflows, giving operators full visibility and control of their assets in one place. This approach has yielded tangible results: operators have achieved 50% faster response times to production upsets and a 30% boost in workforce productivity by using OPX Ai’s streamlined IOC dashboards. By integrating SCADA, PI, and even ERP data into a unified platform, OPX Ai ensures that engineers and managers are all working off the same real-time insights, which improves collaboration and decision-making.
On the maintenance and reliability front, OPX Ai deploys AI-driven predictive models that hook into existing sensor networks. Their asset optimization solutions perform real-time equipment health monitoring (covering pumps, compressors, pipelines, etc.) and can automatically schedule maintenance or alert crews when an anomaly is detected. This has helped clients reduce maintenance costs by about 40% while extending equipment life by 20% through timely interventions. In fact, OPX Ai reports achieving up to 97% accuracy in failure forecasts, allowing operators to fix issues before they cause downtime. Such accuracy builds confidence that the AI isn’t crying wolf – a critical factor for user adoption. The bottom-line impact is fewer unplanned outages and a more predictable, efficient operation.
OPX Ai also excels in production optimization, particularly in the realm of artificial lift and well performance. They offer AI optimizers for gas lift, ESP pumps, plunger lifts, and rod pumps that continually adjust settings to maximize each well’s output under current conditions. One operator saw a 15–25% increase in oil production per well after deploying OPX Ai’s lift optimization, along with a notable reduction in energy usage and pump failures. By integrating these tools with the SCADA controls, the optimization runs 24/7 without needing human micromanagement. OPX Ai’s systems can even perform root-cause analysis on chronic underperformance – for instance, identifying if a particular well’s downtime is mostly due to flowline hydrate formation – and then suggest mitigations. This level of insight and automation directly translates to higher production at lower operating cost.
Importantly, what sets OPX Ai apart is its emphasis on the human factor. Deploying fancy AI software means little if the operations staff don’t use it. OPX Ai recognizes that successful digital transformation is 70–80% about people and processes. They incorporate robust change management and training programs with every project. Rather than just dropping in a new AI system, OPX works closely with operators and field personnel to adjust workflows and build trust in the technology. In one case, a North American operator implemented an AI-driven IOC with OPX’s help and invested in training their field teams on the new tools; as a result, they significantly reduced operating costs (LOE) while boosting production efficiency, because the staff actually embraced the AI insights in daily decisions. This underscores a key point: OPX Ai delivers value not just through tech, but through ensuring adoption. They “foster behavioral change management and implement an operate-by-exception model,” meaning they help reorient how teams work so that the AI and analytics are embedded in routine operations. Front-line operators learn to rely on real-time data and alerts, and management learns to set KPIs that reflect digital performance (like response time, data quality, etc.). By aligning the technology with the workforce, OPX Ai ensures the digital tools actually get used and deliver sustained benefits.
Change Management: The Human Accelerator
Implementing advanced analytics and control systems isn’t just a software upgrade – it’s an organizational change. Studies have found that lack of operator buy-in and poor change management are among the top reasons digital initiatives fail in oil & gas. Simply put, if your engineers and field crews don’t trust the AI or aren’t trained to use new systems, the transformation will stall. Successful digital adoption requires bringing people along for the journey. This means reskilling workers, updating processes, and instilling a data-driven culture from the control room to the well site. Leadership must clearly communicate the “why” of the transformation (not just imposing technology for technology’s sake) and tie it to front-line objectives like safety, production and ease of work. When done right, the results can be powerful. For example, one operator noted that after involving their teams in the design of new AI tools and providing robust training, the staff went from skepticism to actively championing the IOC and analytics – leading to faster issue resolution and a measurable drop in deferred production.
A key aspect of change management is demonstrating quick wins to build momentum. Early in an IOC or AI project, OPX Ai often helps clients identify a pilot scope (say, one platform or a set of wells) to apply the new system and show tangible improvements. This might be catching a pump failure that would have been missed, or optimizing a well’s choke to add a few percent more output. Celebrating these wins helps convert skeptics and reinforces the value of the new ways of working. Executive support is also crucial – when leadership visibly uses the data from the new dashboards in their decision-making and holds teams accountable to data-backed KPIs, it signals that digital is now part of the company’s DNA. In practice, OPX Ai’s engagements typically include workshops to realign KPIs and governance: for instance, instituting regular “operations optimization” meetings where AI findings are reviewed alongside traditional production metrics, ensuring the technology is integrated into management routines.
Finally, change management addresses the cultural resistance that can otherwise doom advanced technology. Oilfield veterans may be wary that AI will replace their judgment, or fear that automation threatens jobs. The reality, however, is that these tools are there to augment and elevate the workforce. By automating routine tasks and providing sharper insights, AI actually frees engineers to focus on higher-value problems and creative solutions. Companies that have embraced this are already building a future-proof workforce – one that’s comfortable working alongside digital tools. In the end, digital transformation is as much about mindset as it is about hardware or algorithms. Those operators who invest in training, communication, and process adaptation are the ones reaping the rewards of streamlined, adaptive operations.
A New Era of Efficiency – and Survival
The push toward AI-enabled, remote-integrated operations is not just an efficiency play; it’s increasingly seen as the only way forward for oil and gas firms to remain competitive in a rapidly changing landscape. Industry-wide, there’s a recognition that maintaining the status quo (siloed teams, purely reactive operations, and under-utilized data) will lead to obsolescence. Only about 17% of large energy companies have fully completed their digital transformation journeys – the vast majority are still in progress or lagging. This means there is a shrinking window for companies to leap ahead by embracing these technologies. Those that delay face mounting costs, safety risks, and an inability to adapt to market shifts. In contrast, early movers are positioning themselves to do more with less – more production with fewer emissions, more uptime with fewer personnel, and more agility with fewer legacy bottlenecks. As one analysis aptly put it, operators that fail to integrate AI and IOCs into their strategy will simply be “left behind” as competitors streamline operations and build a future-proof workforce.
Engaging with a specialized partner like OPX Ai can dramatically de-risk and accelerate this transformation. Rather than attempting a piecemeal approach or getting stuck in endless pilot projects, operators can leverage OPX Ai’s proven solutions and domain expertise to deploy what works now. The business case is robust: companies that successfully digitalize upstream operations can reduce operating expenses by 10–20%, improve production by double-digits, and make their assets safer and more sustainable. But beyond the numbers, this is about resilience. In an industry facing unpredictable oil prices and growing carbon scrutiny, the survivors will be the operators who harness data and AI to run lean, adaptive, and optimized operations. The era of the autonomous, AI-assisted oilfield is arriving – and it’s those who act today, with the right technology and change management, that will still be thriving at the end of this decade. In short, digital transformation is no longer optional; it is the price of staying in the game. Operators that partner with firms like OPX Ai to execute this strategy position themselves to not only prosper through 2030, but to set the competitive benchmarks in the new digital oilfield age.
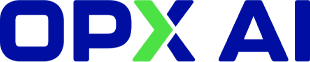
OPX AI is an engineering services company that helps organizations reduce their carbon footprint and transition to cleaner and more efficient operations.
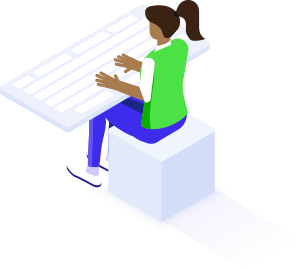